The Indian cement industry, much like its global counterparts, is undergoing substantial transformation driven by sustainability goals and infrastructure development. As this industry transitions, industry leaders are increasingly recognizing the evolving complexities, resource intensiveness, and compliance risks within the supply chain. A recent Capgemini survey has found that 41% of business leaders remain concerned about supply chain vulnerabilities due to geopolitical and environmental risks. In response, 52% are planning to boost sustainability investments, highlighting its critical role in mitigating disruption. Additionally, 61% of organizations are turning to innovation, sustainability, and technology as critical drivers for future success, recognizing the existential threat posed by unsustainable practices.
The built environment accounts for a staggering 40% of global CO2 emissions resulting from fuel combustion and contributes to 25% of global greenhouse gas (GHG) emissions. Within this statistic, cement production emerges as one of the highest-emitting industries, accounting for approximately 7% of global CO2 emissions. To combat climate change effectively, the world strives to achieve net-zero emissions by 2050, making rapid decarbonization of the cement and concrete industry imperative. With cement and steel together accounting for 15-20% of India’s total emissions and heavily reliant on fossil fuels, these “hard to abate” sectors pose significant challenges in achieving the nation’s net-zero target by 2070. Addressing the emissions from cement production is critical for several reasons, including the scale of cement consumption in India. Consumption is massive and, if left unchecked, its emissions could surpass those of the electricity sector, intensifying the country’s carbon footprint.
The industry’s shift towards sustainability is further reinforced by the UN’s 17 Sustainable Development Goals (SDGs), which aim to address climate change, human rights abuses, and environmental degradation. Regulatory frameworks, such as India’s BRSR Core, are being enforced to align with these goals, emphasizing greater supply chain transparency and a focus on environmental, social, and governance (ESG) factors.
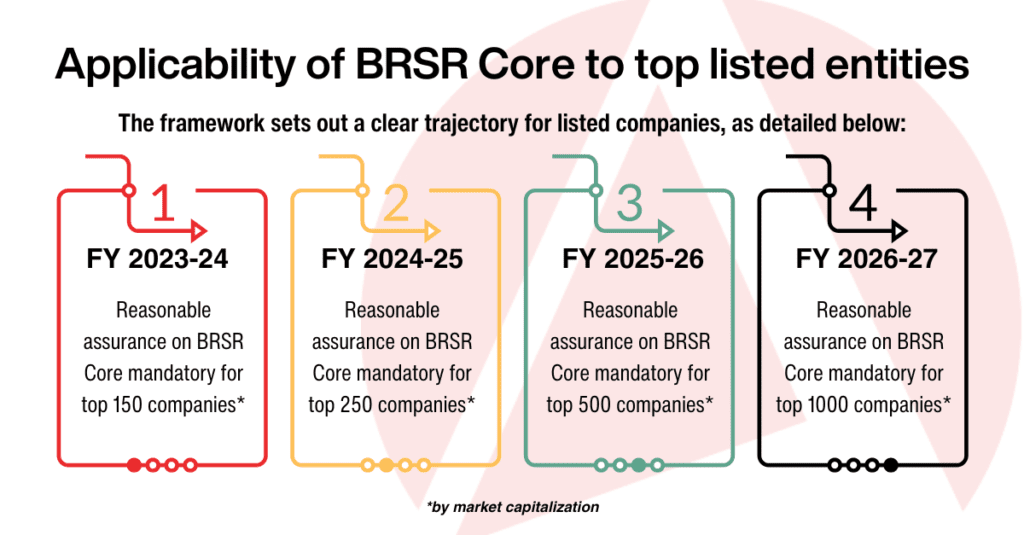
The obvious solution is to turn to technology, but what is the best approach? Many cement industry leaders may believe that their procurement and supply chain management processes are already as transparent and optimised as they can be, but on further investigation, the reality is often a web of spreadsheets, old-fashioned forms, and manual data entry processes even to maintain supply chain management and reporting at current levels – alongside some significant gaps. Often, the reality is that these error-prone, costly, time-consuming systems and processes are anything but efficient and fail to deliver the level of reporting confidence that is increasing required.
Truly efficient and robust end to end supply chain management must include:
- Data capture from multiple sources, in different languages and formats
- Meticulous data checking and verification
- Comprehensive risk assessment
- Demonstrable risk mitigation
- Real-time access to data and reporting
- Supplier performance statistics
- Integrated new supplier onboarding process.
While utilization of an ERP and spreadsheets does remove some manual effort, it is becoming harder and harder to meet business and compliance requirements in this way. The ongoing maintenance of running manual processes and spreadsheets leads to high total cost of ownership (TCO). Often much of that is below the surface as an opportunity cost, so it’s never fully accounted for, but most procurement teams recognise it as a massive burden and a distraction from higher value activities. So, what is the alternative?
More and more companies are shifting away from managing suppliers within their ERP and spreadsheets. Instead, they are looking for specialized solutions where data can be managed, analysed and reported in a controlled but flexible environment. Data can then be shared with the ERP for general business and procurement needs.
When should you consider a third-party supply chain due diligence solution?
While some ERP solutions offer supply chain management, they are usually just one small piece in an ERP’s broad array of solutions. This means that developing and updating them to keep up with changing supply chain legislation and stakeholder reporting requirements may not be a major area of focus or investment for the vendor. They won’t include the data collection, validation and analysis that is so central to the new wave of supply chain legislation.
Simple spreadsheets may be a good fit for businesses with less complex supply chains, lower levels of stakeholder scrutiny and fewer reporting requirements, but when managing major complex large scale projects, ERP + spreadsheet type solutions are unlikely to provide the data validation, due diligence or risk analysis required. They are also likely to increase the need for manual workarounds and carry the risk of failing to meet increasingly stringent reporting requirements.
If a business opts for an in-house developed solution, it can be difficult to maintain as supply chain obligations evolve. The constant development often becomes an unwelcome distraction for an IT team that wants and needs to be focused on the core business. Businesses often find, what starts out looking like a cost-effective solution quickly starts to incur unforeseen management costs to update and maintain systems, or a need to hire additional headcount to handle the required manual efforts.
With all these solutions, you will also be placing increased pressure on your suppliers who will have to fill out your forms and comply with your processes as well as those of all the other businesses they supply.
How to choose the right supply chain due diligence solution for you
As you evaluate your current supply chain due diligence processes, you should consider three key areas that can greatly impact your organisation, now and in the future:
- Complexity: How complex or fragmented is your supply chain? Do your suppliers stretch across countries and continents? Do you buy from countries where language is a barrier to communication. How up to date is your supplier contact information and how good is your supplier engagement really?
- Risk level: Major infrastructure projects often involve layers of sub-contractors making it challenging to maintain standards. It can also be hard to find suppliers with the credentials to meet your requirements and project timescales. How much do you source from markets where environmental and social standards may be an issue.
- Reporting requirements: What sort of reports do you need to produce to meet stakeholder, investor, and regulatory requirements? How will you keep track of regulatory changes? How does the solution handle ongoing changes and modifications. Are manual interventions required?
Small business to mid-market supply chain management | Mid-market to multi-national supply chain management |
---|---|
Minimal supply chain complexity | Complex supply chains |
Small businesses to mid-market | Mid-market to multi-national corporations |
Low risk operations | High risk operations |
Less regulation | Increasing regulation |
Lower number of reporting requirements | Higher number of reporting requirements |
Low public scrutiny | Increasing public interest |
Low reputation impact | High reputational impact |
It can be tempting to rely on lower-cost AI generated or web-scraped information, but instances of forced labour, child labour, and environmental pollution are rarely found on the internet until they become the subject of a media exposé. If you are working internationally and are exposed to increasing legislation, only by using local knowledge and connections, working closely with NGOs and undertaking site audits and worker interviews in the highest risk locations will you ever hope to get close to the level of understanding you need.
Taking the next step
In-house or light touch supply chain risk management solutions may be a good fit for smaller, less complex organisations with simple value chains, lower risk operations, and less regulatory and public scrutiny but the supply chain processes of cement organisations with its high focus on health and safety, carbon and other sustainability concerns operating in highly regulated environments and a supplier chain that spans international borders are, inevitably, more complex and the need for better data, greater analysis and more automation and greater compliance will only increase.
If you’re ready to consider the benefits of a professional supply chain management solution, consult the ratings and reviews of the available options on the market or talk to one of our experts today.